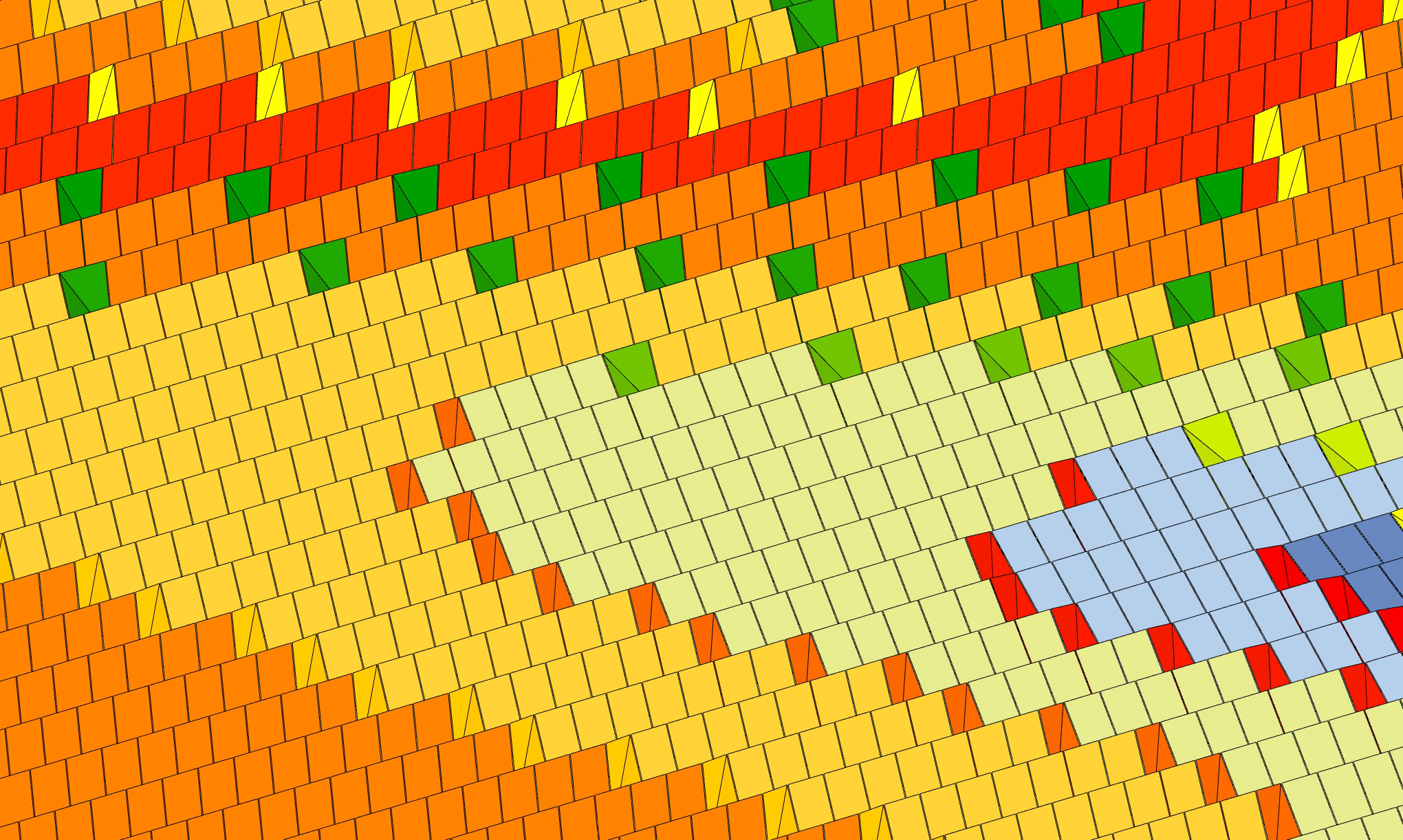
LisbonHotel
LisbonHotel is an already existing hotel that is being renovated by the architect offices A2M. This project involves some Grasshopper magic for its new facade design where around 3000 metalic pieces are used to shade the inside of the building while revelating a drawing of Lisbon's hills.
In collaboration with A2M in Brussels, I’ve received the opportunity to work on the facade of an existing hotel. Sadly, most of the design phases were almost already finished and my work consisted in rationalizing the design bellow in a parametric way in order to make some changes in seconds while tracking and exporting data of thousands of pieces.
I used the word “sadly” because I hoped we could optimize interior confort/consomptions with these shading elements, but we ended up building a model a close to the apparence of the one below as possible.
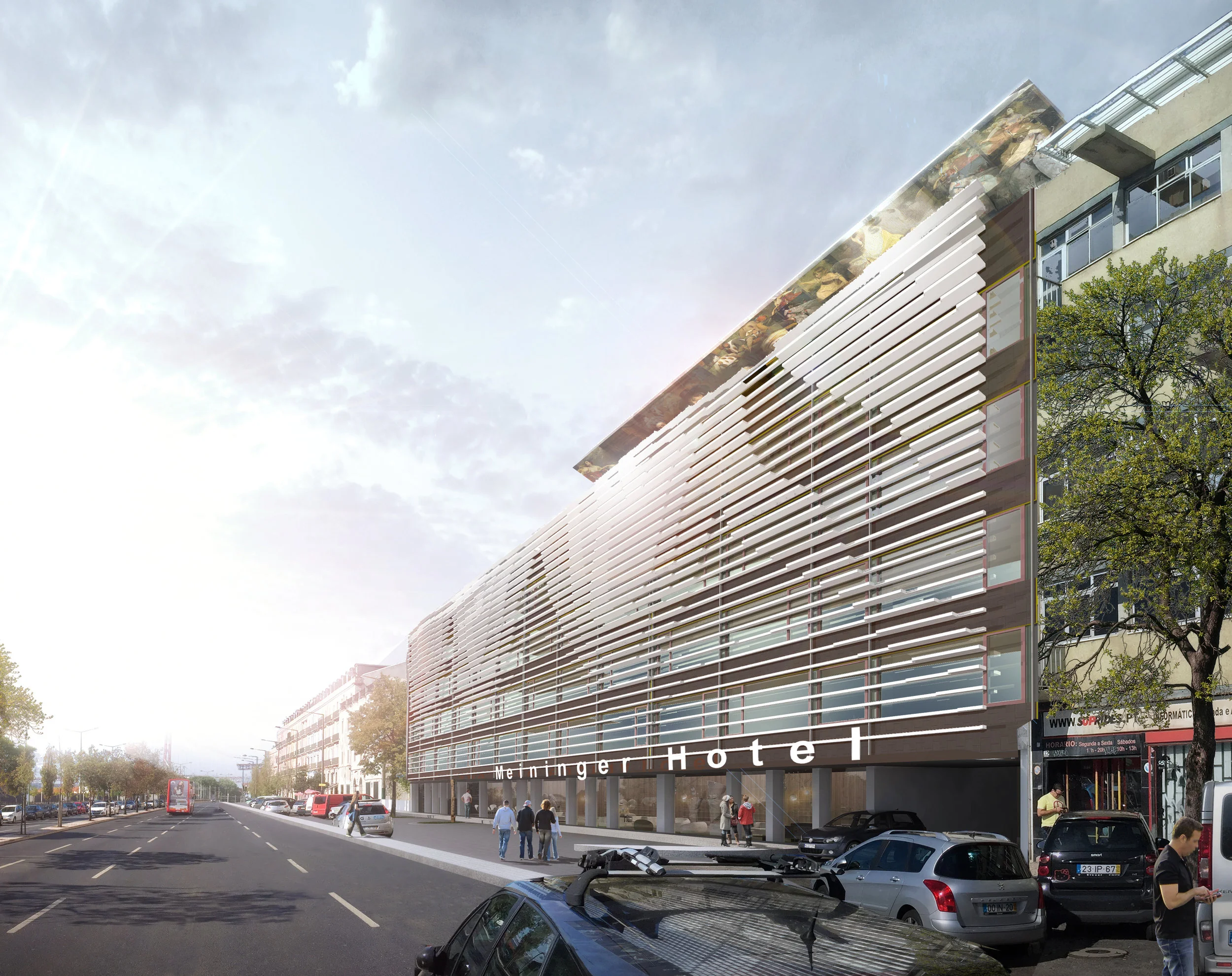
Render : UCS for A2M (early design)
As a team work, we first started thinking about a way to make this facade constructible in real life. We therefore opted for metallic pieces that would be folded to be able to match the drawing in the facade of the previous image, as well as for self structural purpose. Here under an early drawing of the concept, with transition pieces between the ones with different angles.
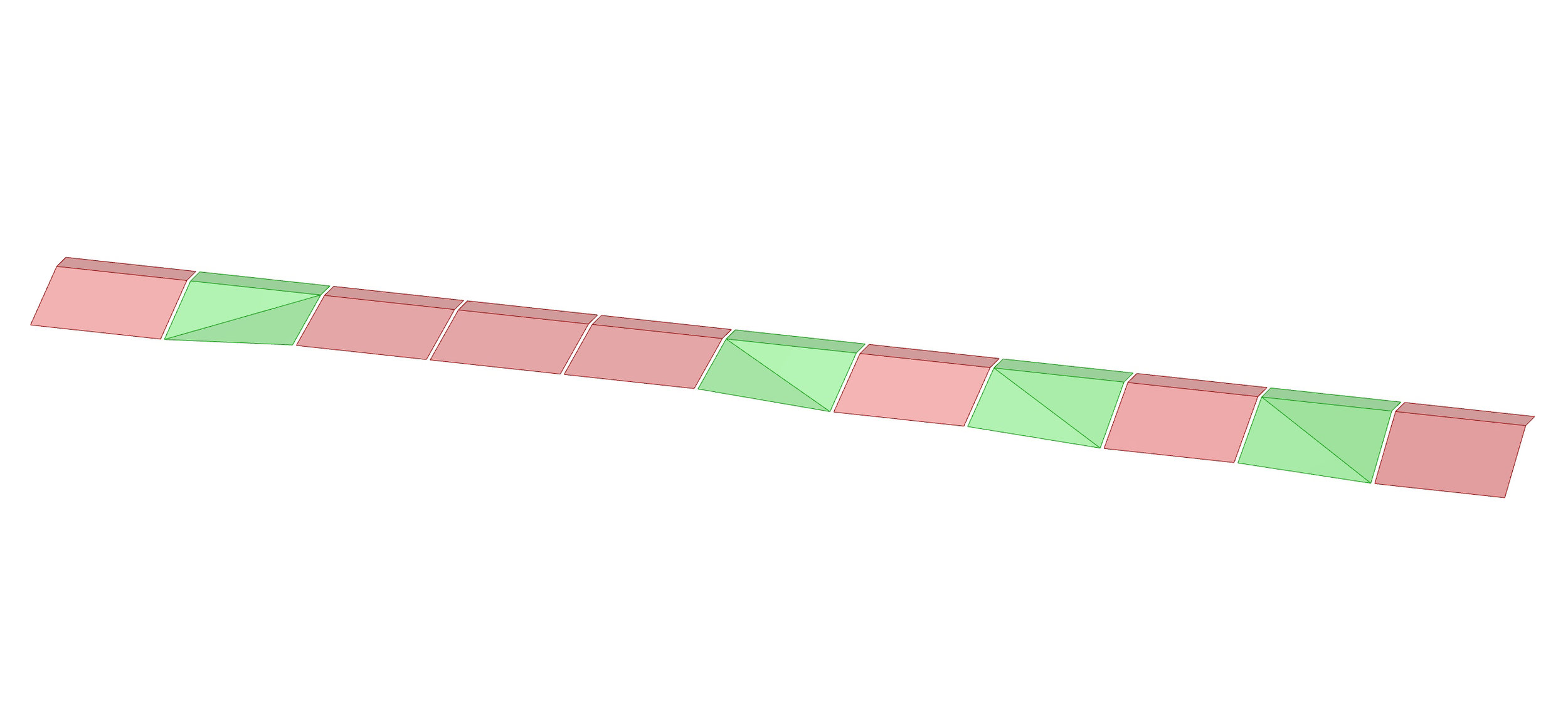
After this system was approved by the team, I started building the parametric model as flexible as possible.
As the drawings of the facade where based on the actual landscape of the city, I decided that the contour lines would be the starting point. The drawing below shows the logic behind their use in the model. It’s shown for a small row of shading elements, but this would actually be tested with a rather large grid of points, one for each piece (almost 3000). A folding angle is chosen by the architects, and is multiplied by the number of time each point is tested inside of a contour line.
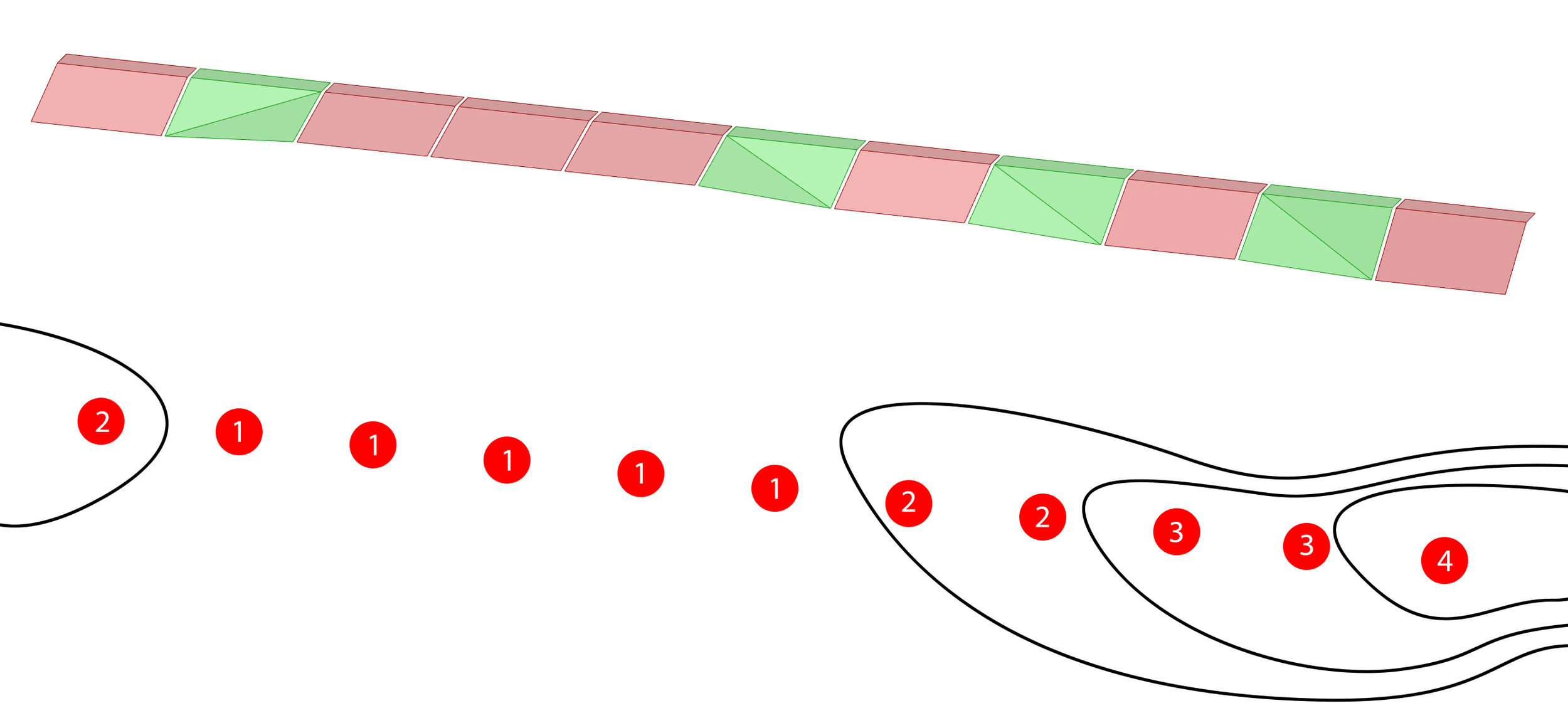
After some Grasshopper fun, the parametric model was complete. As all the dimensions / angles of the shading were not completely defined yet, I tried to keep it as flexible as possible while making it optimized in terms of computation speed. It is actually capable to evaluate the position of almost 3000 points within (or not) multiple contour lines, categorize them, create 3D model based on dimension/angle parameters, display fancy colored clusters, extract unique pieces, unfold their geometry, mesure the dimensions/angles, export all the needed data in spreadsheet plus an export to dxf format… In around a second, every time.

The whole facade with all its shading components.
Here above, all the shading elements are clustered by their type (one fold or two), their angles and their dimensions. As any parametric model would do, any value can be changed, any contour line can be modified, the 3D model updates and exports itself automatically. At all time, their number and position on the facade is tracked as the picture below illustrates. If anything is changed, these are also automatically updated. They also receive individual label that will be further used for construction purposes.

All unique pieces unfolded
If we continue to zoom in, we have more information about all the unique pieces. As the fabrication process will be almost entirely automated (cutting and folding), I had to export some values (the angles) in a spreadsheet, and the dimensions as a dxf format. Their displaying on the rhino viewport is just fancy to watch, but was actually useful to double check the results directly, without switching between softwares.
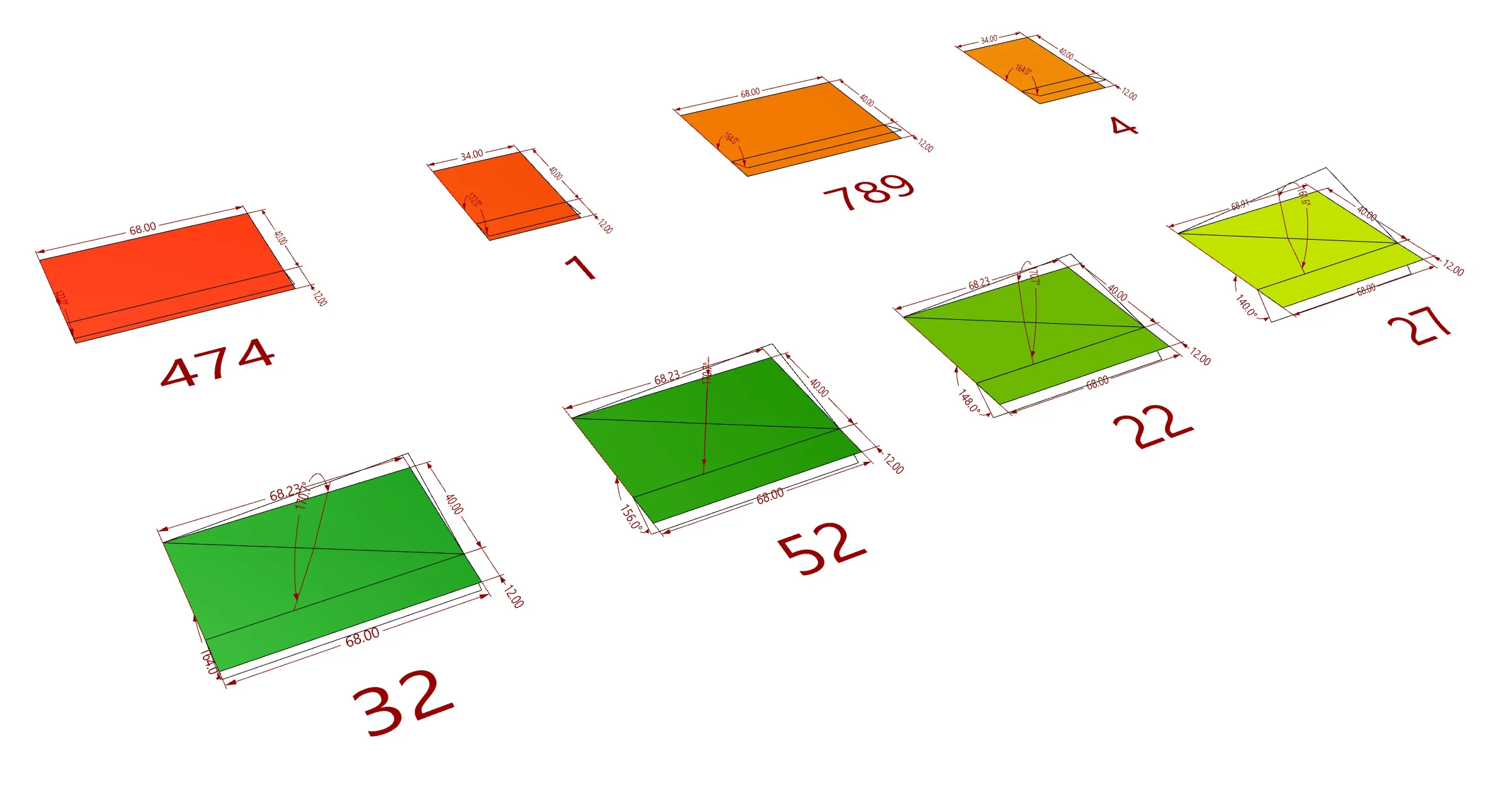
More documents will come as the project continues and as prototypes are tested. Despite the lack of real optimizations, this project gave me the opportunity to work closer to the construction phases of the project, where all the data has to be precise and correct. Here under the picture of the (rather small) definition as its current state.

Antoine -